近20年来,纤维增强热塑性复合材料以其优异的韧性、可修复和可回收性,引起了工业界广泛的研究。目前工业中纤维增强热塑性复合材料的成型方法大多为热熔法,包括树脂膜法、树脂粉末法、混纤法、预浸料与半预浸料法。这一类成型方法主要关注树脂高聚物的热成型性能,辅以高温高压成型复合材料。由于树脂是大分子长链,本身流动困难,浸渍纤维困难,从源头决定了复合材料性能不高。于是,热塑性复合材料的原位聚合成型技术以其低成本、高性能等特点成为最新的研究热点。
通过对树脂聚合过程的研究,包括树脂聚合过程中温度、压力等参数对树脂聚合的影响等,为纤维增强热塑性复合材料原位聚合成型技术的应用奠定了基础。使用合适的树脂与引发体系,在纤维周围原位聚合高聚物,从而制备性能优异的热塑性复合材料。对PA6(Polyamide 6)树脂的阴离子聚合研究起始于19世纪30年代,这一体系对于反应条件参数的控制与反应洁净度要求非常高。对这一问题的研究催生了最早的密封混料设备,进一步发展出结构反应注射 SRIM(Structural reaction injection molding )与真空注射VI(Vacuum Infusion) 成型技术。这些技术保证了反应环境的清洁度,对于温 度压力的控制非常精细,能够满足这一高性能材料的成型要求。同时将成型周期缩短至数分钟,大幅提高了生产效率。对PMMA(Polymethyl methacrylate )树脂原位聚合制备大型结构件的研究主要集中于其热量传导方面,制备厚制件与大尺寸制件过程中传质传热问题非常突出。研究者设计了种类繁多的引发体系,关注了其诱导时间、凝胶时间点等反应动力学过程。同时,一部分研究者关注了热量传导的模拟,预测了制备复合材料的最大厚 度。这些研究共同推动了 PMMA 树脂原位聚合成型技术的发展,使用这一方法成功制备了大型整体船身结构。另外,学者们还研究了 PBT( Polybutylene terephthalate)等结晶性树脂在聚合过程中的结晶性能变化,为该类树脂的成型提供了理论支撑。
本文综述了纤维增强热塑性复合材料原位聚合成型技术的研究进展,详述了几种较为常用的成型技术,热塑性树脂传递模塑 T⁃RTM (Thermoplastic resin transfer molding)、结构反应注射 SRIM 与真空注射 VI, 分别讨论了使用这些技术的研究实例,分析了每种技术的特点与关键点。概述了几种热塑性复合材料原位聚合成型技术的其他方法。最后,综合讨论了纤维增强热塑性复合材料原位聚合成型技术的共性问题,展望了纤维增强热塑性复合材料原位聚合技术的发展趋势.
引言
相较于热固性复合材料,纤维增强热塑性复合材料具有韧性高、成型周期短、制备效率高、可回收和二次加工的优点,这使其不仅满足了军用领域对高损伤容限性能的需求,还满足了民用领域对降低成本、提高生产率的需求,这些年逐渐成为科研领域的研究热点。纤维增强热塑性复合材料的制备方法从原理上可分为两大类:一类是发展较早的热熔方法 ,一类是原位聚合方法。
热熔法一般需要高温高压来驱动长链高分子树脂流动浸渍纤维,由于树脂粘度较大,微观尺度树脂很难完全浸渍纤维,导致产品局部孔隙含量较高,留下较多的缺陷。
原位聚合方法使用低粘度单体或寡聚物前体浸渍纤维,有以下几点优势:(1)由于树脂粘度低,不需要高温高压条件即可获得比目前可达到的熔体处理工艺更大、更厚、更集成的产品,如图1所示;(2)可以获得树脂对纤维浸渍优良的制件 (制件质量更均一、力学性能更优);(3)由于树脂聚合发生在纤维表面,故纤维与树脂间能够形成较强的化学键连接;(4)可以在织物增强的基础上,添加纳米粒子到未反应的单体中,获得分布均匀的纤维增强聚合物纳米复合材料;(5) 工艺周期更短,生产效率高。
图1 两种工艺制备的各类树脂粘度分布
纤维增强热塑性复合材料原位聚合的成型方法大多来源于热固性复合材料已经发展完善的成型方法,一些成型方法与原有方法基本一致,另一些方法在原有基础上针对热塑性树脂的特点进行了较大改动,这些不同源自于热塑性树脂与热固性树脂特性之间的显著差异。热塑性树脂和热固性树脂聚合速率均随温度的升高而增加,然而,一些热塑性树脂具有半晶性质,结晶受到温度的影响 。当温度过低时,结晶速度过快,反应链末端和单体在聚合之前就被困在晶体内;当温度过高时,结晶度降低,导致聚合物强度、刚度和耐化学性变差。另外,一些反应性热塑性材料,如 PMMA(聚甲基丙烯酸甲酯)、PA6(聚酰胺 6)、PA12(聚酰胺 12) 和 PBT(聚对苯二甲酸丁二醇酯),其熔体粘度比普通热固性树脂低一个数量级。因此,纤维预成型体在浸渍过程中产生的毛细力较大,充模过程中可能形成孔洞和流道。
最早用于制备复合材料的原位聚合法是铸造成型,这种方法工艺简单且成本低,适用于制造大型产品 。由于技术的快速发展,该方法已难以适应目前使用连续纤维或者织物作为增强体的现状。本文综述了纤维织物增强的热塑性复合材料原位聚合成型方法,包括热塑性树脂传递模塑(T⁃RTM)、结构反应注射(SRIM)、真空注射(VI)、树脂膜熔渗(PFI)等。针对每种成型方法, 本文综述了主要的应用实例以及相关研究前沿进展,评价了每种方法的特点。
艾邦建有复合材料产业交流微信群,欢迎产业链上下游朋友识别二维码,从公众号底部菜单加入群内交流探讨!
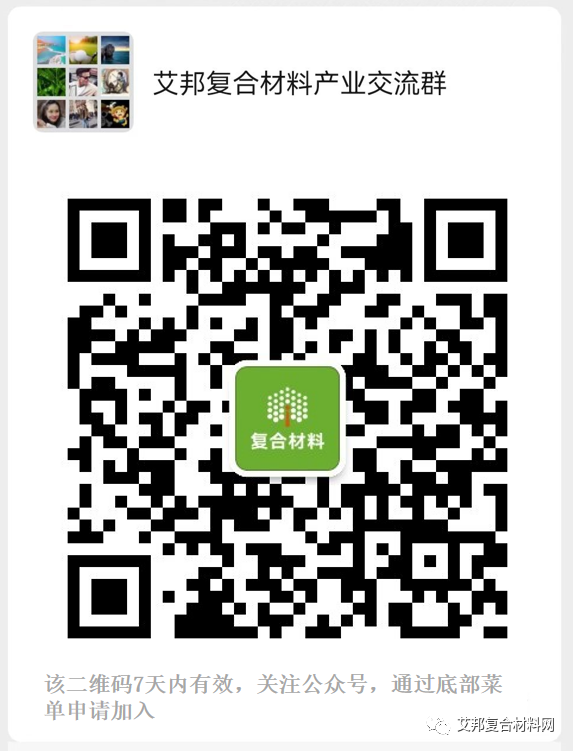
01
纤维增强热塑性原位聚合成型技术
本章着重从织物增强热塑性原位聚合成型技术方面展开,详述了几种原位聚合成型技术。从技术发展概况、使用实例以及技术特征等角度讨论了热塑性原位聚合成型技术, 并进一步对使用其他形式增强体的工艺进行了讨论,以供对比分析。
1. 树脂传递模塑 T⁃RTM
在生产纤维增强热塑性复合材料时,主要考虑的是基体树脂的粘度。如果能充分降低热塑性塑料的粘度,热塑性树脂转移模塑(T⁃RTM)等热固性树脂生产技术可用于热塑性复合材料的加工,如图 2 所示。Mairtin 等提出了使用液体浸渍方法时,树脂需要满足的三点要求:(1)树脂粘度低于 1Pa·s ;(2)完成浸渍后,树脂能够在短时间内发生化学或物理变化,达到硬化;(3)最终树脂性能满足制件需求。Luisier等在其基础上增加了第四条要求,即反应无副产物生成。
图2 T⁃RTM 成型工艺
Parton等遵循这四条要求,选择Cyclics公司的 CBT 前驱体作为基体树脂(锡基催化剂),选择两种玻纤织物作为增强相,使用真空辅助T⁃RTM 工艺制备复合材料平板(尺寸为 320mm×200mm×2mm)。设定真空度从0.14 MPa到 0.08 MPa,控制充模时间,如图3所示。考量了树脂组分搅拌时间、充模时间对复合材料板材制备质量的影响。研究发现,对于这种工艺窗口很短的树脂体系,较长(从 12 s 延长至 30 s)的搅拌时间会导致复合材料浸渍不充分。进一步对浸渍充分的试样进行了弯曲性能测试分析,发现单向玻纤复合材料的弯曲强度为 775 MPa,略低于理论预测值 850 MPa,原因是制件中有一些区域的孔隙率达到 4.2%。Parton 等的研究开拓了热塑性复合材料的液体成型方法,且他们得出了一些重要的结论,如对于工艺窗口较小的树脂体系,工艺参数的控制极为重要,需要精确设定。
图3 T⁃RTM 工艺流程
Achilias 等推导了扩散控制的反应速率模拟计算公式,详细论述了自由基聚合过程中的动力学机理。2015 年, Alexander Zoller 等最早开始研究 BPO(过氧化苯甲酰)/ DMA(二甲基苯胺) 室温引发 MMA(甲基丙烯酸甲酯) 树脂的聚合动力学模拟。2017 年,美国科罗拉多大学的 Suzuki 等以 MMA 树脂为基体、玻纤为增强体,研究了树脂聚合的动力学 ,并引入了一维热传导方程建立板材传热模型, 模拟计算了不同厚度板材的温度历程。同时, 他们还使用室温引发的氧化还原体系,以 BPO 为氧化剂、 DMT(二甲基对甲苯胺)为还原剂,采用 T⁃RTM 工艺制备了复合材料,并用红外摄像机对板材成型过程中的温度进行了测量。结果表明:引发剂浓度提高使凝胶效应提前,峰值温度变高,与模型预测值较为吻合,如图 4 所示。他们实验测量了传热系数, 将现有的 MMA 聚合模型与一维传热模型联立,同时考虑了效率因子,模拟了树脂反应的温度变化历程,合理捕获了初 始浓度改变时的诱导时间和最大温度。他们进一步运用这 一模型预测了板材的最大厚度(在他们的实验条件下是40cm)。Suzuki 等同时验证了预溶解 PMMA 的量对聚合动力学的影响。实验发现,随着预溶解 PMMA 的量增多,凝胶效应逐步提前。
图 4 不同引发剂浓度的模型预测(实线) 与实验结果(虚线)对比
Charlier 等分析了用于复合材料液体成型(LCM)的丙烯酸反应性混合物特性,以制备用于复合材料的热塑性基体,并研究了自由基聚合过程中的转化率、复粘度和固化放热性能。结果表明,这一体系存在凝胶效应,聚合具有较高的放热性。流变学研究表明,LCM 工艺的可注射单体转化率为 10%左右。Charlier 等还建立了甲基丙烯酸甲酯/ 聚甲基丙烯酸甲酯混合物的玻璃化曲线,以确定单体完全转换所需的热条件,从而调控残余单体含量。使用这种基于丙烯酸的反应溶液进行快速 LCM 成型是可行的,因为在 90℃下,反应 5min 内可以得到完全聚合的树脂基体。
Boumbimba等研究了丙烯酸原位聚合制备玻纤织物增强复合材料的低速冲击性能,以及少量丙烯酸嵌段共聚物的添加对该树脂混合物原位聚合的影响,并进一步分别在 20 ℃ 、80 ℃和 -80 ℃下分析了嵌段共聚物添加量对复合材料低速冲击性能的影响。结果表明,在 20 ℃ 和 80 ℃ 时,共聚物的添加能够提高复合材料的冲击破坏阈值,尤其是 80 ℃ 条件下,最高提高了 24%。但在 -80 ℃ 条件下,共聚物的加入反而使复合材料的冲击吸收能有所降低。
美国伯明翰大学的 Barfknecht 等在 2016 年提出了一 种新的原位聚合制备 APA-6 复合材料的思路,通过将引发官能团沉积到增强纤维上,之后仅注入单体组分进行原位聚合。该技术所需加工设备简单,污染风险较低,极大提高了复合材料原位聚合的自动化程度。用硅烷衍生引发剂(N-[5-(Trimethoxysilyl)-2-aza-1-oxopentyl]caprolactam )对玻璃纤维表面引发聚合进行了研究,发现这一聚合方法能够在纤维表面形成 PA 原位聚合的引发点,但是制备的板材中心部位树脂单体未完全转化。
最近,Louisy 等使用丙交酯树脂作为基体,玻纤织物作为增强体,通过 T⁃RTM 工艺制备了 120 mm× 120 mm×5 mm 的复合材料板材。分别在实验室条件和生产条件下研究了催化剂添加量、温度对纯树脂聚合的反应时间、转化率、分子 量、分子量分布的影响。研究发现,在实验室氩气保护环境中,反应时间为 12 min,聚合度达到 91%~ 97%;而在空气环境中,反应时间延长至 40 min,树脂的摩尔质量下降了一半以上,说明大气环境对这一树脂体系的聚合产生了较大的影 响。Louisy 等进一步研究了添加玻璃纤维使用 T⁃RTM 制备复合材料对树脂聚合的影响,发现玻纤对树脂聚合程度的影响很小,树脂仍能在足够的反应时间下达到较高的转化率。不同的是,模具中的树脂聚合反应无法搅拌(实验室中反应伴随搅拌),因此聚合时间延长至 2~3 h,聚合物分子量也有所降低。
综上,热塑性复合材料的 T⁃RTM 工艺作为热塑性复合材料原位聚合的首要方法,能够制备质量较好的复合材料。同时,该方法较成熟、效率高且成本低。然而,与热固性 RTM工艺相比,仍需要注意以下几点:
(1) T⁃RTM 工艺需要对反应参数进行更加精确的控制,这基于对树脂反应动力学的研究更加全面和深入。
(2)对于一些反应热较大的树脂体系,仅从工艺或反应物浓度单方面进行研究已经不能满足工业需求,需要从新的引发体系、反应物浓度、反应动力学、工艺参数控制和传热模 拟共同考量,综合研究出适合的原位聚合方法。
(3)一些生产中的实际环境因素与实验室有所区别,对树脂聚合有不小的影响。
1. 结构反应注射 SRIM
结构反应注射工艺与热固性复合材料的 RTM 工艺密切相关,如图 5 所示。该工艺与 RTM 工艺相同的部分是纤维增强体均放置在两个硬模具之间,后期树脂注入浸渍纤维进行聚合。不同的是,这个工艺为了防止树脂过早的聚合,增加了反应物料输入系统,反应性树脂组分被分离,在进入模具前进行定量混合,使用高压(0.8~1 MPa)浸渍干纤维。
图5 结构反应注射工艺原理图
结构反应注射成型方法最早是 Karger-Kocsis 等于 1992 年提出的。他们使用玻纤织物增强尼龙嵌段共聚物原位聚合制备了复合材料,采用光镜和声发射(AE)同时监测的方法研究了玻璃纤维(GF)束毡增强尼龙嵌段共聚物(NBC)的破坏模式。结果发现:在裂纹萌生阶段(最大载荷阶段)和裂纹扩展阶段,其破坏模式存在较大的差异。前一阶段裂纹尖端钝化,后一阶段纤维毡网状变形,并伴有相应 的脱粘、纤颤和组成纤维及其细丝的断裂。当超过最大载荷时,基体的变形模式由韧性屈服转变为粘性撕裂。
2013 年,PPG 公司从商业角度报道了使用 SRIM 工艺制备 APA-6 玻纤复合材料的优势:由于实现了实时混合物料,可以极大地缩短树脂混合与充模时间,工艺周期缩短至 3min,每天可生产 500 件产品;相比于金属构件减少了 50%的质量;制备的复合材料内部质量优良、无空隙,玻纤含量可达 70%,力学性能与环氧相当,可以用于结构件。
德国恩格尔奥地利有限公司研究了 SRIM 工艺制备复合材料车身结构的性能,发现 APA-6 之所以能够被广泛用于热塑性液体成型工艺的原因是:这一树脂在室温时为结晶固体,在达到熔点 70℃ 后能够非常迅速地转变为粘度约 10 MPa·s 的液体。这一特性使得 APA-6 能够充分浸渍增强体纤维,使得制备的复合材料内部质量优良。
结构反应注射充模工艺具有如下优点:
(1)工艺周期非常短,通常在工业生产中仅为3~5 min;
(2)反应条件洁净;
(3)工艺参数控制精确,反应物预热,计量混合均为机械控制。
但是,此工艺缺点也很明显,如设备成本高,实验室研究难以承受等。
3. 真空注射 VI
真空注射工艺与 VARI 工艺类似,充模速度较低,大气压力足以使模具夹紧,因此最大可实现部件尺寸仅受反应体系的时间限制。在混合了两罐中的原料后,反应性混合物被注入到一个缓冲容器中,用来分离注入所需的压力和促进输液所必需的真空,如图 6 所示。
荷兰代尔夫特理工大学的 Rijswijk 团队最早开始进行真空注射成型工艺的研究。他们在制备风电叶片的项目(2005年)中, 研究使用了新的树脂体系 APA-6 来替代环氧,以期降低制造成本。这一想法基于这一团队前期对 APA-6 阴离子聚合过程的熟知(他们在2003 年对 APA-6 的引发体 系进行了研究),对于不同配比的引发剂组分与形成的聚合物性能有了较为详细的数据储备。由于 APA-6 的阴离子聚合对实验条件的洁净度要求很高,他们自制了一个简易的混料设备,如图7所示。Rijswijk 首先研究了引发剂和催化剂添加量对树脂聚合反应的影响,随后研究了 APA-6 的工艺温 度与压力的可调范围,获得了合适的工艺流程,分别制备了 玻纤和碳纤增强的 APA-6 原位聚合复合材料,其综合力学性能略低于环氧复合材料。
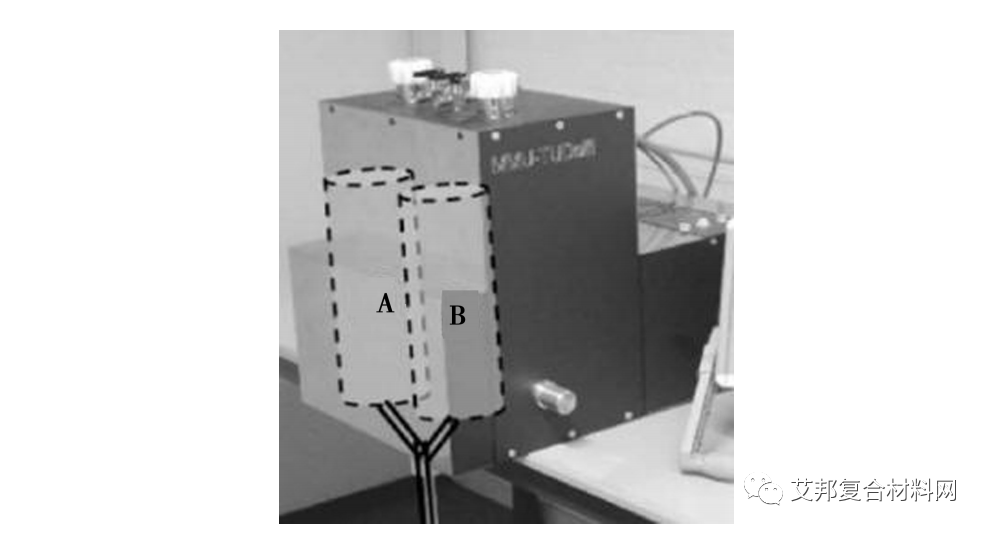
图7 微型混料单元
Rijswijk 等进一步研究了聚合温度对真空注射制备 APA-6 板材质量的影响。结果表明,聚合温度的提高对单体转化率影响较小,但是随聚合温度从 140℃ 升高到 170℃ ,分子量从 42000 提高到了 90000,密度与孔隙率也有小幅提升。这些影响综合反映在树脂板材的力学性能上,其中在 150 ℃聚合温度下得到的材料强度和模量最高,这可能与 PA 的结晶性能有关。
中科院宁波所的颜春等在 Rijswijk 团队研究基础上, 探讨了APA-6 原位聚合方法的引发体系添加量以及复合材料的力学性能,重点从结晶的角度对其力学性能进行了分析。研究结果表明,随着聚合温度从 140℃ 升高到 180℃ ,连 续 GF/APA-6 复合材料基体树脂的结晶度从 52.7%逐渐降低至 36.1%。当聚合温度为 150 ℃ 、聚合时间为 45 min 时,其 力学性能达到最高,拉伸强度为538.1 MPa,弯曲强度为 497.2 MPa,层间剪切强度为 52.5 MPa。中科院宁波所还对 CBT 开环聚合致脆的机理进行了研究,发现 CBT 的开环聚合 致脆原因主要是树脂前体纯度问题,在熔化聚合时,由于单体熔化温度不同,导致一部分熔点高的单体被包裹在已反应的长链分子中,形成铆钉作用。对此,他们对树脂前体进行提纯,使所有树脂前体同时熔化和聚合,解决了这一问题。
西班牙的Agirregomezkorta等近几年研究了真空注射工艺参数对 CBT 复合材料冲击性能的影响。使用了碳纤维作为增强体,制备了 250 mm×250 mm×3.6 mm 的板材,主要研究了两种非等温工艺条件对材料性能的影响,其中一种是短周期快速冷却(熔点以上保持 5 min,33℃/ min 降温速率),另一种是长周期慢冷却(熔点以上保持 1h,3.5℃/ min 降温速率)。一方面,在结晶收缩过程中,快速冷却会在富树脂区域产生随机分散的孔隙。另一方面,缓慢冷却材料的内部没有孔隙,但结晶度较高,因此材料较脆。由于基体的脆性和纵向收缩的共同作用,富树脂区出现了许多微裂纹。慢冷复合材料的临界分层能略高于快冷复合材料的临界分层能,而快冷复合材料在渗透前吸收的能量比慢冷复合材料高 25%以上,表现出较低的脆性。
VI 工艺的优点主要有以下几点:(1)生产的部件大小几乎不受限制;(2)加入了物料混合系统,能够制备对反应条件非常敏感的树脂;(3)需要的压力较低,一般为一个大气压或更低;(4)成本低;缺点是模具通常只能使用一次,并且产品一侧的表面质量较差。
4. 其他工艺
本节包括一些研究较早、目前应用较少或方法特殊的热塑性复合材料制备工艺,包括但不限于纤维织物作为增强体。
4.1 树脂膜熔渗
树脂膜熔渗(Resin film infusion ,RFI)类似于热固性复合材料的预加工:在模具中交替堆叠纤维层和未反应的活性树脂混合物层。施加热量和压力时,薄片熔化并浸渍纤维, 之后聚合开始,如图 8 所示。由于薄膜没有足够的力学性能,需将其直接铺覆在支撑纤维织物上,同时也可以使用粉末浸渍的织物。在熔化和浸渍过程中,铺层体积大幅减少, 通常需要多个压实步骤来压缩铺层。在这种情况下,反应性混合物的粘度同样需要低于1Pa·s。较厚的部分压实困难,通常需要两面刚性模具,加上较大的压力,同时使用低粘度的低聚物前体。
图8 树脂膜熔渗工艺
RFI 的主要优点是安装简易和快速浸渍,而缺点是增加了压实过程。
4.2 反应注射拉挤
热塑性反应注射拉挤工艺(Thermoplastic reaction injection pultrusion)是最近才成为人们感兴趣的制备方法,如图9 所示。这一工艺的材料和设备开发最新进展及其巨大的商业潜力,激发了人们的兴趣 。该工艺是使用连续纤维作为增强体,将反应性的热塑性树脂实时混合加入模腔中,边浸渍纤维边聚合。在模具的后端进行冷却,直接连续成型所需形状的型材。
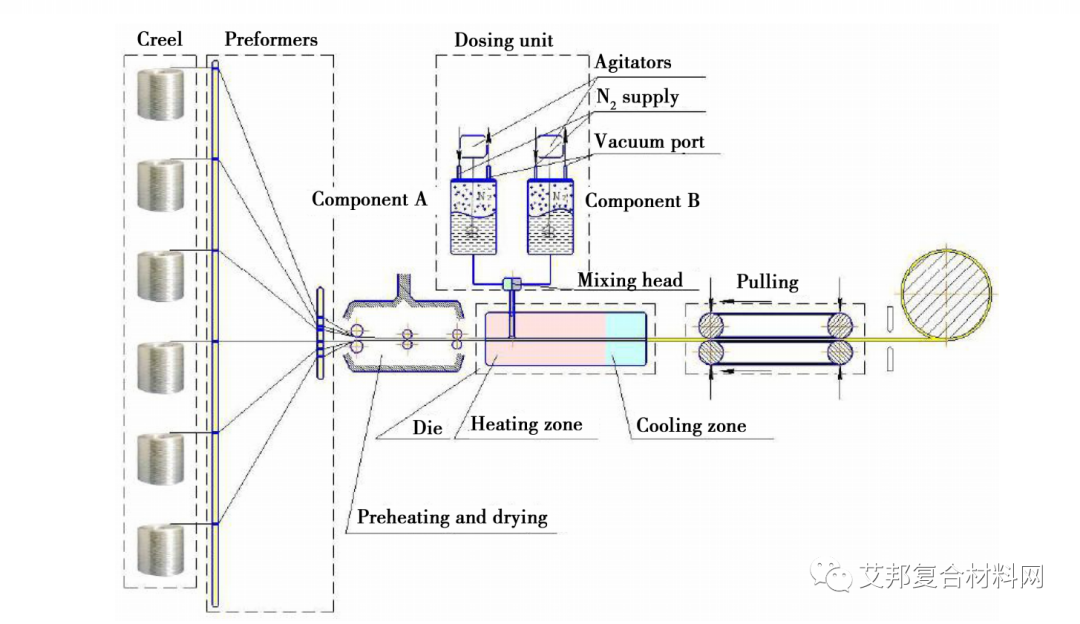
图9 反应注射拉挤
德国斯图加特大学的 Epple 等研究了反应注射拉挤成型玻纤增强 PA-6 复合材料的成型性能。他们选择活化剂浓 度为 2.5%,催化剂浓度为 3.75%,制备了复合材料型材,如图10 所示。结果表明,采用反应注射拉挤法可生产出连续的玻璃纤维增强 PA-6 零件。为了评价反应注射拉挤工艺生产的零件质量,必须在进一步的试验中分析成型过程参数的影响。
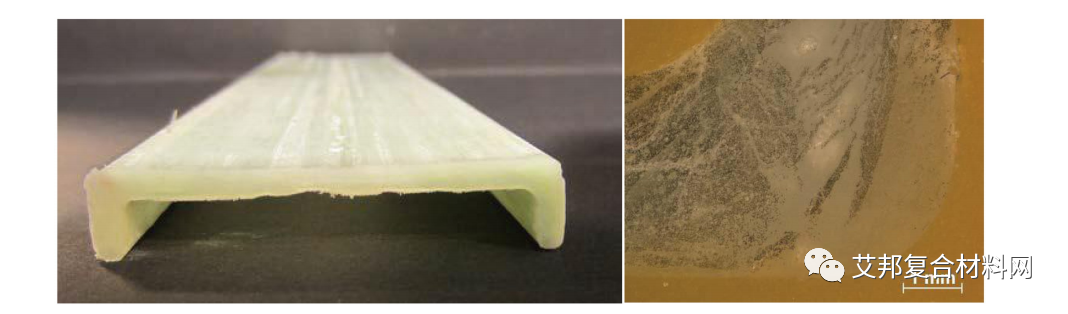
图10 反应注射拉挤制备的玻纤增强 PA-6 复合材料
KraussMaffei 等公司合作开发了一种名为 iPul 的拉挤系统,生产速度达到 3m/min(热固性材料的速度通常是0.5~1.5 m/min )。CQFD 复合材料公司等合作为现代汽车开发了拉挤前碰撞梁, 此前碰撞梁使用了单向玻纤增强的阴离子聚合 PA-6 基 体 。这些成功的开发项目证明了其工业应用的可行性。然而,该工艺的流程开发和参数优化是关键问题,需要进行全面研究,目前其还未得到商业化应用。
反应注射拉挤优点是可以连续生产无限长度的复合材料产品,生产效率高,同时具有热塑性材料的优越性能。缺点是设备成本较高,制备的制件必须具有相同的截面。
4.3 增材制造 AM
增材制造(Additive Manufacturing ,AM) 在 2010 年就有报道提及,使用了内酰胺的阴离子聚 合。Khodabakhshi等采用传统的引发剂(NaCL, CLMgBr=) 和活化剂(n⁃乙 酰己内酰胺),通过差示扫描量热法(DSC)测试,确定喷墨的 最佳配方和条件。使用 AM 法的树脂体系凝固半衰期可缩短至1 min以内。他们还比较了喷墨 PA-6 与铸型 PA-6 的性 能,发现喷墨 PA-6 的转化率、分子量和结晶度分别为 95%~ 96 %、41~50 kDa 和 38%~40 %,而铸型 PA-6 的转化率、分子 量和结晶度分别为 94%、45~52 kDa 和 43% ~44%。
增材制造的优点是能够制造任意形状的制件,且得到的制件内部质量均一,内应力小。缺点是原料成本高。
02
结语与展望
综合以上各类纤维增强热塑性复合材料原位聚合成型方法的特点,可以得出一些区别于热固性复合材料共性的点:
(1)部分热塑性树脂粘度较热固性树脂低一个数量级, 在充模过程中需要重视毛细作用,以免产生流动不均导致的缺陷。这一问题需要对树脂流变,聚合动力学进行更深入的研究,探究合适的树脂体系配比,以及更精细的工艺参数。
(2)热塑性树脂的制造追求更短的制造周期,以期提高效率降低成本,这对一些放热量较大的树脂体系提出了不小的挑战,因此工艺中的热量控制成为一个重点。这一问题的解决有赖于对树脂聚合动力学和传热过程的综合考量,以及设备的改进。
(3)很大一部分热塑性树脂具有半结晶性,加工这类树脂需要注意结晶与工艺温度之间的关系。因此,工艺后端的降温过程对这些树脂来说异常重要。
(4)界面是复合材料制造和研究中非常重要的部分,成型过程中对这一问题考虑较少,对界面的研究大多集中在实验室。热塑性复合材料的上浆剂研究起步较晚,尚无大范围应用的产品,这一问题的解决依赖于热塑性复合材料产业的发展。
原位聚合热塑性复合材料方法由于成本低且绿色环保, 逐渐成为工业界关注的热点。20 世纪初,荷兰发展的风电项目要求制备 3000个兆瓦级的风力发电桩,由此引发了 APA-6 原位聚合方法的大规模研究,开创了这一领域的研究潮流。国际对于汽车工业发展复合材料部件的减轻质量、降低能耗的需求催生了 PBT 树脂原位聚合方法的研究热潮。同样,海洋设备与船舶的发展需求大尺寸构件的制备技术,也会推动热塑性原位聚合方法的研究。而航空工业对高韧性材料的需求也成为研究这一方法的坚实基础。
对于纤维增强热塑性复合材料的原位聚合成型方法的研究,已经呈现出井喷的态势。一方面,对于既有的树脂类型更加深入地研究其聚合过程,以及新型的引发体系和聚合方法;对于更多高性能树脂,研究摸索其可以制备的基本方法。另一方面,对于已有的工艺方法进行不断完善和改进;对于新的成型技术进行开发,例如反应注射拉挤、增材制造与热塑性复合材料焊接与修复技术。
艾邦建有复合材料产业交流微信群,欢迎产业链上下游朋友识别二维码,从公众号底部菜单加入群内交流探讨!
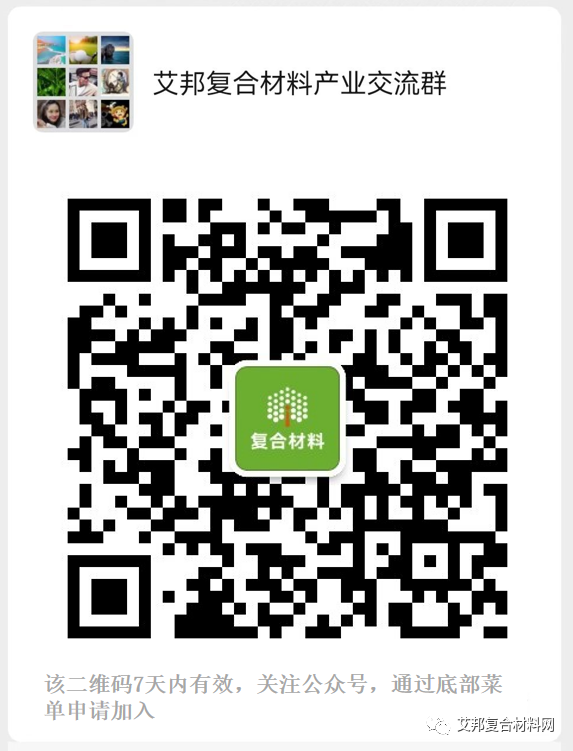
2023-03-16
2023-03-03
2022-12-05
2022-11-28
|
|
|
|
|
|
|
|
|
|
|
|
|
|
|
|
|
|
|
|
|
|
|
|
|
|
|
|
报名方式:
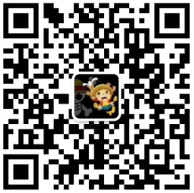


原文始发于微信公众号(艾邦复合材料网):纤维增强热塑性复合材料原位聚合成型技术研究进展
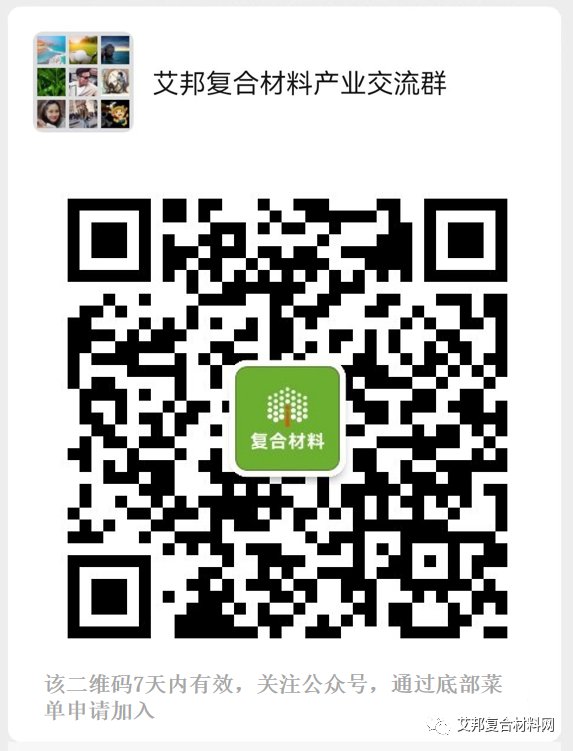