01
背景
随着轨道交通行业的快速发展,碳纤维复合材料因其重量轻、强度高及刚性大等优势应用越来越广泛,对于降低车辆噪声、振动,提高安全性、舒适性,减少维修等均有重要作用。
02
碳纤维复合材料应用现状及问题
目前,大部分的厂商应用的主要是热固性复合材料部件,如转向架、司机室、设备舱以及内饰件等等,用更轻、更坚固、耐腐蚀的复合材料替代传统的金属部件。
价格 生产效率 阻燃
是阻碍复合材料在轨道交通领域大规模应用的三大拦路虎
比如传统的热固性碳纤维复合材料首要解决的便是轨道交通领域严格的防火要求,如欧盟的EN 45545防火标准,对点火、自熄能力、火焰蔓延、烧穿、热释放、烟雾产生和烟雾毒性等众多性能指标都有严格要求。对于热固性塑料,满足EN 45545防火标准通常有两种选择:
-
第一种复合材料表面添加防火涂层,涂层会增加重量,并且使用寿命有限,需要根据使用要求重复喷涂,费时费力。
-
第二种是在树脂基体中添加阻燃剂,这也会影响增加重量,同时对整体材料性能产生不利影响。一文了解树脂改性中常用的添加剂和填料
03
24%连续碳纤维,76%回收短切碳纤维结合模压工艺
德国CG Rail公司通过使用24% 连续碳纤维、76%回收混合碳纤维和模压工艺相结合,在满足消防安全、强度和重量要求的前提下,最大程度的降低了成本,成型周期缩短到2分钟,重量降低了30%。
04
项目开发完整过程
材料筛选
第一阶段分别进行了火焰传播、热释放、烟雾不透明度和毒性测试,需要满足的特定列车类型的要求设定。
第二阶段是温度性能和稳定性评估,在火车需要承受的环境温度范围内(从-40°C 到约 80°C)对材料进行测试。
第三阶段测试材料对环境的影响。这些材料经受了热、水蒸气、盐雾和紫外线的照射,实质上是在进行加速老化实验,满足30年的寿命要求。
第四阶段是材料性能测试,这些包括满足静态拉伸、压缩、开孔拉伸、压缩、平面内剪切、层间剪切以及冲击测试。
第五阶段是疲劳性能测试,数百万次负载循疲劳性能测试。
零件设计:仿真和建模
侧壁盖板本身的设计过程与材料测试同时进行,一旦选择了最终材料,零件设计就会相应地进行调整。大多数建模和仿真工作是使用Altair的 OptiStruct 和 HyperWorks 软件。
制造设计
相比与模压成型,注塑成型更加适合批量化的制造,由于该零件每年需求量在数千件,同时注塑模具太贵而暂时选择模压成型工艺。
考虑到制造过程,设计团队采用了仿真优化设计,并针对成本和可制造性进行了调整。例如,仅在需要增加刚度的地方放置材料,优化模型包括沿结构侧面的一系列肋,重新设计了肋骨,使其具有均匀的厚度和间距,以便于制造。
建模模拟需要连续纤维的强度特性,因此决定可以在其余区域使用成本较低的不连续纤维。特别是肋条,需要不连续的纤维材料——连续纤维在压入模具腔体时会起皱,而不连续纤维在成型过程中更容易流动。
上模具
下模具
预浸料片材切割
预浸料放入底部模具
最终零件
05
未来前景
热塑性复合材料侧壁盖创新的轻量化解决方案满足了客户对性能以及消防安全的所有要求,而且将重量减轻了30%,来可以使用类似的材料来制造用于铁路或其他终端市场的各种耐火热塑性复合材料部件。
往期推荐
原文始发于微信公众号(复合材料加工与制造):热塑性碳纤维复合材料在轨道交通领域最新应用——高铁设备舱侧壁板
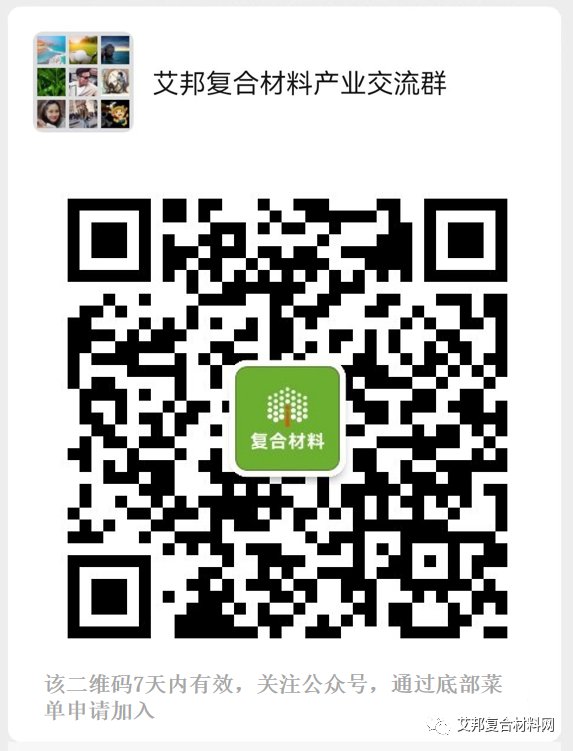