绝缘件为玻璃纤维增强复合材料,绝缘件的外形轮廓和尺寸如图1所示,绝缘件由筒身和两端的连接部位组成。
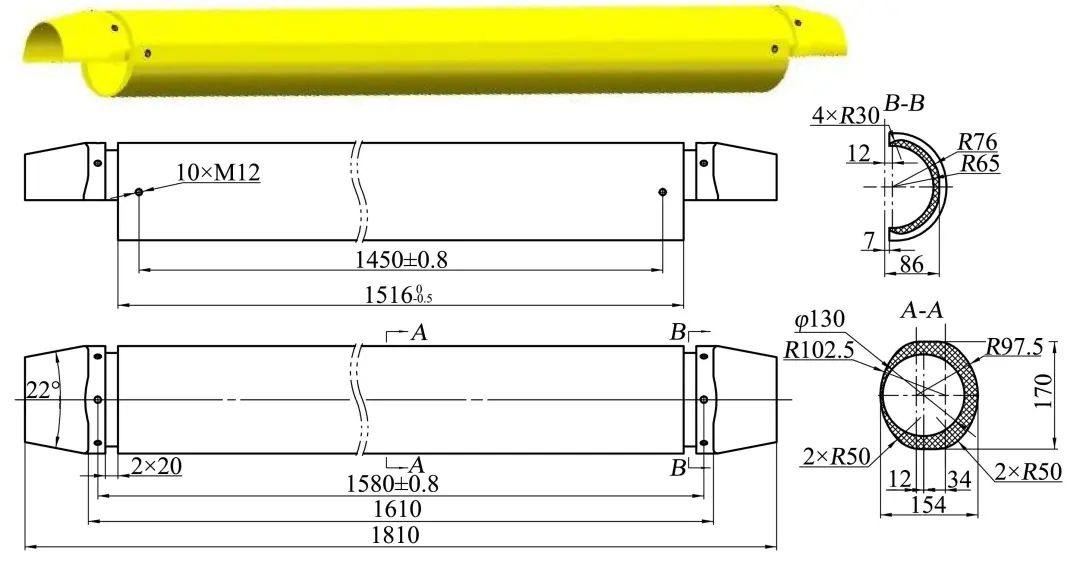
图1 绝缘件的外形及尺寸
复合材料绝缘件为核磁共振测井仪部件,体积较大,其作用是排除泥浆,使探头附近的泥浆相对较少,减少泥浆中影响测井效果的氢原子。在使用时除满足其基本的力学性能要求外,还要求耐温200 ℃、耐压170 MPa,同时具有耐腐蚀、高耐磨等特性。复合材料绝缘件由于薄壁区域的存在,皆达到上述指标要求存在一定的困难,所以选配合适的材料和工艺体系是保证成型制品各项性能的前提。
根据绝缘件的使用要求,经过优化的钢模RTM灌注工艺路线如图2所示。
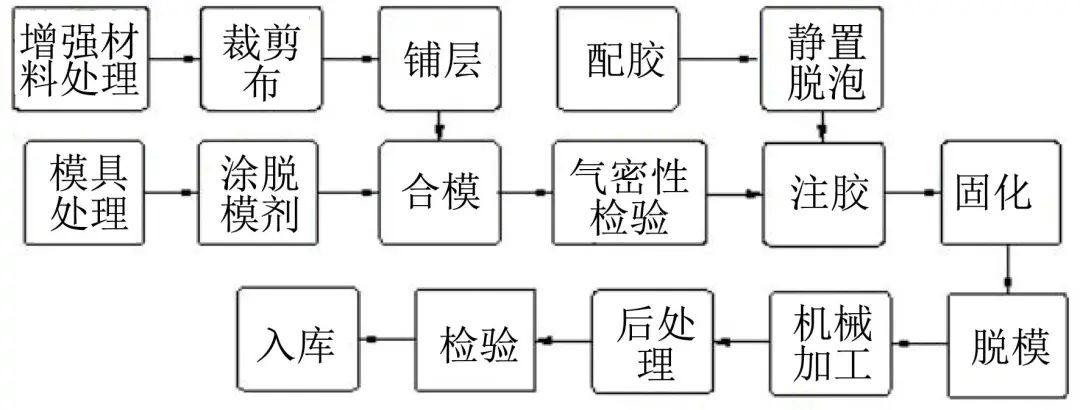
图2 绝缘件成型工艺流程
为保证成型制品的力学性能及其他综合性能,制品在RTM灌注成型过程中应避免出现含量高的树脂区,故应对纤维编织物的铺层进行设计,纤维布的铺层截面如图3所示。采用多层纤维布堆叠铺设,每层布厚为0.2 mm,为确保所铺布层的规整度,铺设过程中对织物进行缝合或用纱线勒紧,铺设编织物时需沿芯轴的中心线对称。铺布过程中尽量少用喷胶,必须用时采用点喷喷胶方式。铺设过程中应确保作业现场在无尘、无污染及干燥的环境中进行。
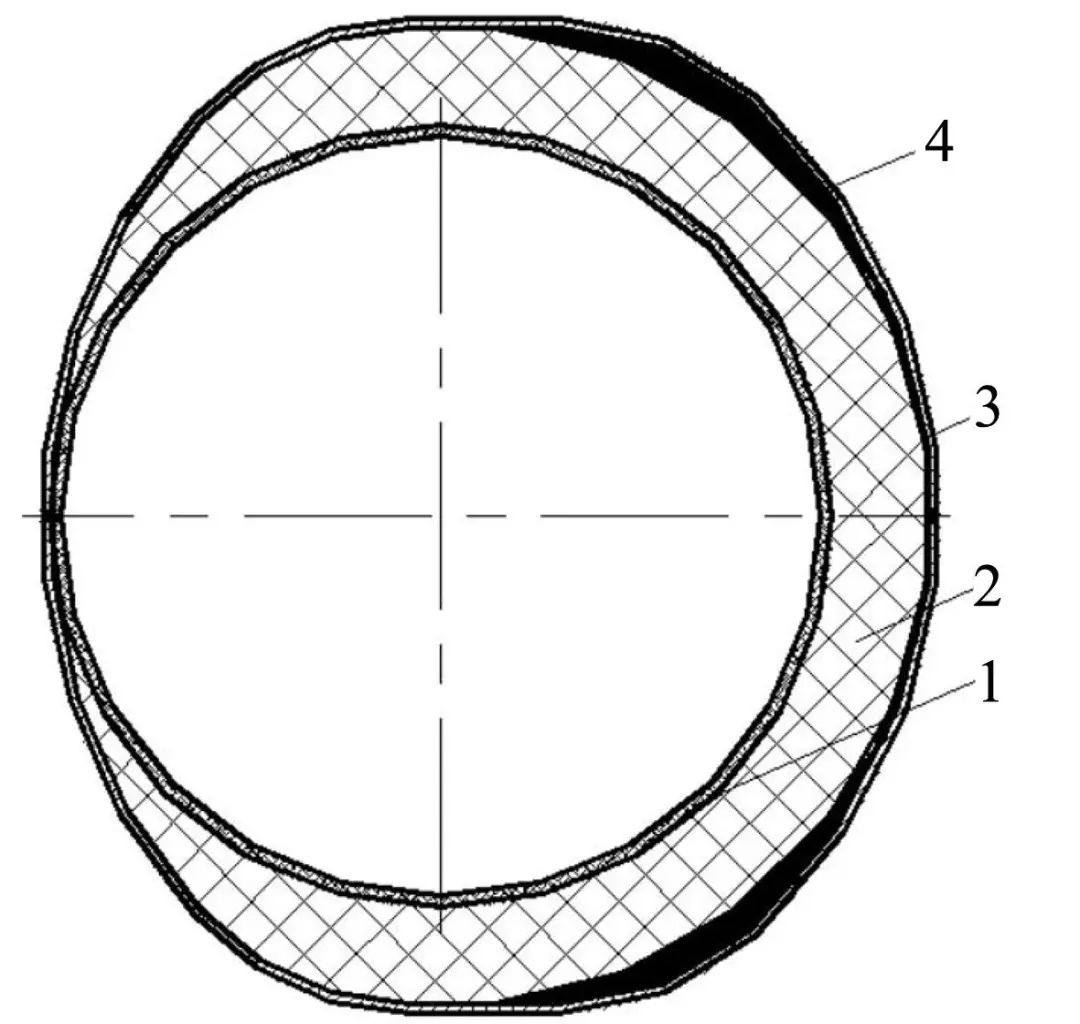
图3 织物铺层截面1.内圈铺层 2.中间铺层 3.外圈铺层 4.局部铺层
模具各模块之间合模精度要求高,应设有辅助脱模装置,保证成型制品能顺利脱模;在注射压力下模具有足够的强度和刚度,是保证其密封性能的前提;为保证型腔内树脂流动的合理性,需设计浇口和排气口,模具的总体结构如图4所示。此外模具零件材质选取还应考虑树脂固化放热峰值的温度对模具的影响。模具整体的密封性是RTM灌注的关键,上、下模及端盖的密封结构如图5所示。
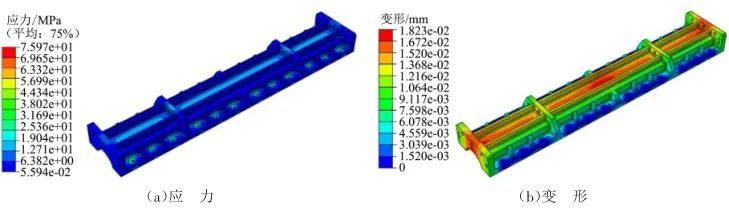
图4 模具整体结构
1.出胶口端盖 2.芯轴 3.成型制品 4.下模5.上模 6.入胶口端盖
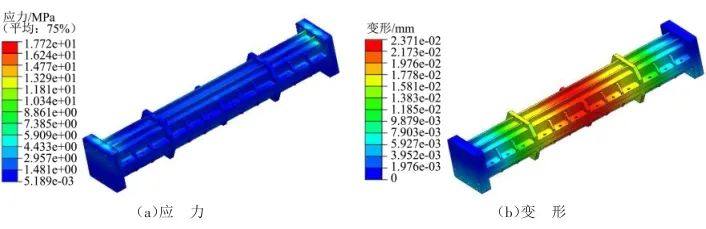
图5 模具密封结构
工作状况主要是考察纤维编织体在芯轴上完成铺层后,将预制体装入密封模具型腔内,合模时纤维编织体对模具的反作用力。分析时将模具的上、下模连接的12组螺栓孔表面固定,在上模的内表面垂直施加20 kN的总压力,经计算最大应力值为76 MPa,且为螺栓孔口的应力集中,如图6(a)所示,小于许用应力260 MPa,最大变形发生在沿模具截面方向的中部,且变形由两端向中间逐渐增大,最大变形量为0.018 mm,如图6(b)所示,小于极限挠曲变形量0.4 mm,结构满足要求。
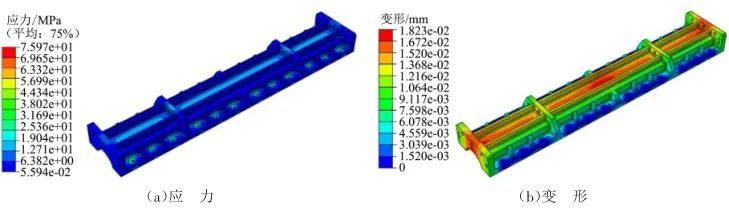
图6 模具合模的应力与变形仿真结果
通过计算模具最大应力值为17 MPa,小于许用应力260 MPa,最大变形发生在沿模具长度方向的中部,变形由两端向中间逐渐增大,最大变形量为0.023 7 mm,且是模具在没有安装芯轴的基础上,小于极限挠曲变形量0.4 mm,如图7所示,模具结构刚度满足要求。
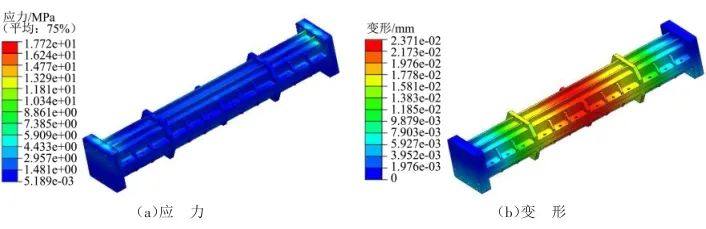
图7 简支工况成型模应力与变形仿真结果
RTM工艺在灌注完成后要进行高温固化,这时需考虑树脂固化放热峰值的温度对模具产生的热影响。热源输入从模具的外表面通过热传导进入模具的型腔,温度为170 ℃,模具材料的导热系数为52 kW/(m·℃),热膨胀系数为1.5×10-5/℃,经计算模具由于温度产生的热变形为0.29 mm,且未考虑芯轴和制品对模具的支撑作用,模具热变形云图如图8所示。
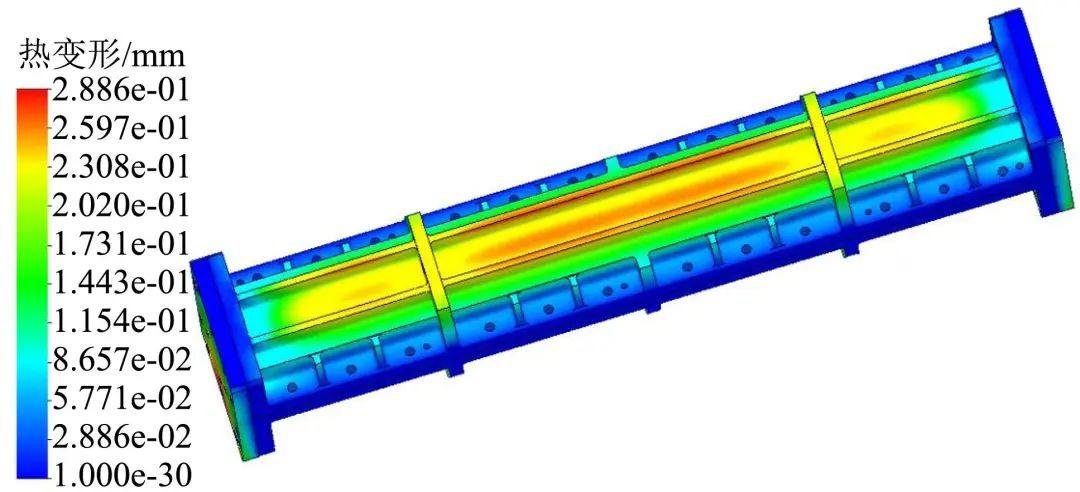
图8 模具热变形
绝缘件按规定工艺完成铺层后将其装入模具密封型腔内,卸下两端辅助工装、合上模具,连接浇注系统进行注射,如图9所示。按总体成型工艺流程生产脱模后,制品表面光滑,无褶皱现象、无缺陷,最后对制品的两端进行切割、打孔、去飞边处理,生产的制品如图10所示。
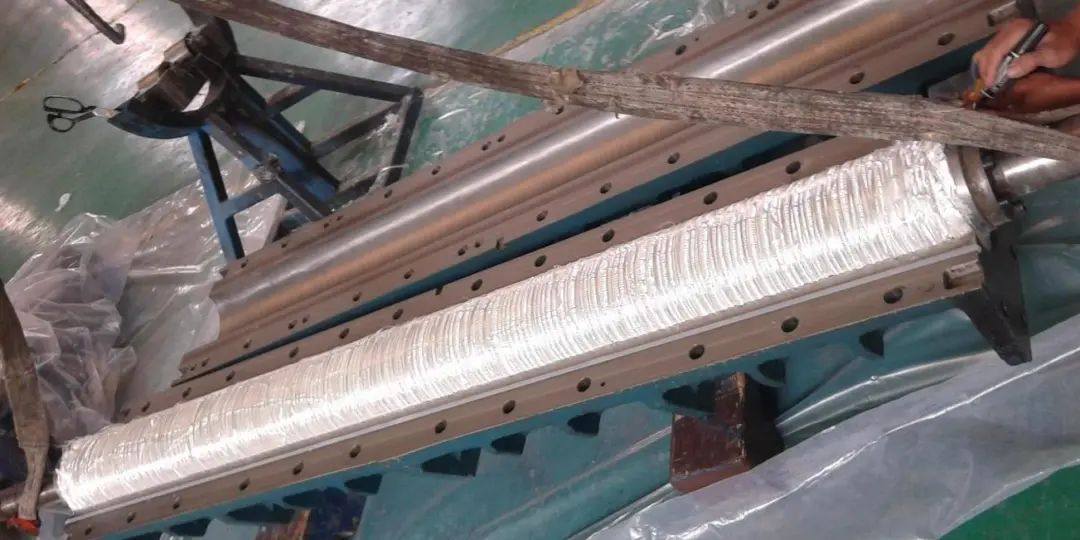
图9 绝缘件生产
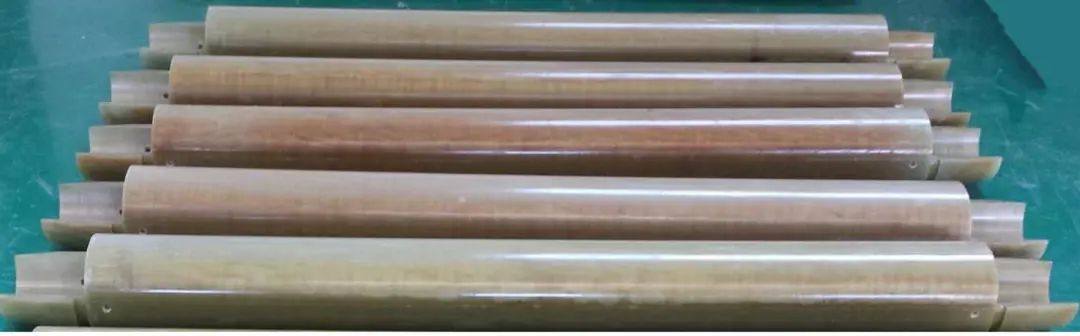
图10 绝缘件制品
▍原文作者:南无疆1,成子兴1,冯胜標1,王礼先2,吴瑶3
▍作者单位:1. 太原科技大学 重型机械教育部工程研究中心; 2. 青岛泓捷模具有限公司 ; 3. 北玻电力复合材料有限公司